Licenses of the Product Design and Manufacturing Collection have access to not only Inventor and its add-ins, but also to Autodesk Fusion. This means that as a PDMC license holder, you have access to two different CAM platforms. In this blog, we will break down the main differences between the two, and advise on what to consider when choosing between the different applications.
Due to the continued development of Autodesk Fusion, the availability of tools and licensing required around them, may change as time moves on. All information below is correct at the time of writing in May 2024.
Inventor or Fusion CAM?
This is a question we get very often, and our answer usually boils down to two main factors:
- Design Workflow
- Machining Requirements
Both products follow the same flow in creating machining toolpaths, and publishing posts. So, there is always the options to start in one and move to the other at a later phase as the workflows evolve. They also have interchangeable Tool and Post Processor libraries, making the transition between the two much easier.
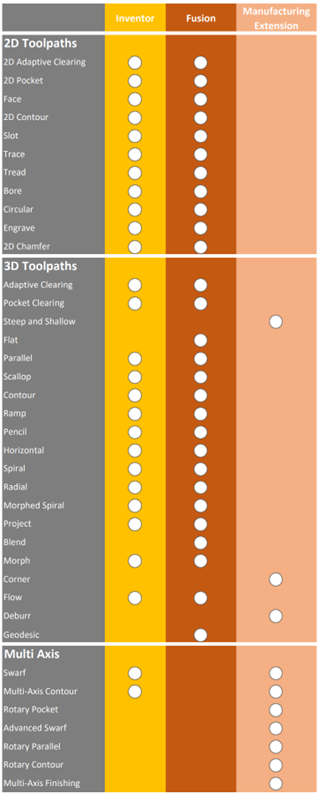
Design Workflow
The main thing to be aware of when using Fusion CAM from Inventor is the translation of the file from Inventor to Fusion. When imported into Fusion, the files are currently converted into a Fusion design file. Meaning there isn’t a live link between the Inventor model and Fusion. This also means that Fusion will not be aware of the Feature Tree in the model, and therefore only sees the model as a solid body with surfaces, rather than features. However, this isn’t all that bad if you want to separate the Design model from the Manufacturing model. Or have two different departments for Design and Manufacturing.
When using an approval process we already have a point in at which the design cannot change. After this point we no longer expect the model to update and are able to work without a linked model. This also means that if our machinists need to change the model to get a better finish within the design constraints, they can do so without worrying about changing the source of truth.
Designing in Inventor, Machining in Inventor allows you to push live updates to the CAM toolpaths, meaning any changes to the model are directly adjusting the toolpaths. This is great for adjusting the design to improve the toolpaths. We can also simulate toolpaths at this point to ensure the model is manufacturable. Using a Data Management system, like Vault, once the design has been approved we can lock the source file and work on a separate manufacturing model in the CAM environment.
Designing in Inventor, Machining in Fusion will mean the model is no longer linked to the source file. Which works well once our model has been approved and is ready for manufacture. Our machinists can then work on the file without worrying about updates as they will only ever have a released or approved version in Fusion. This can be tied into a Data Management system, like Vault, where we only send files to Fusion once the design has been approved.
Machining Requirements
Fusion CAM offers 2.5 to 3+2 Axis manufacturing capabilities within the base product. This is extended to 4- and 5- axis capabilities with the Manufacturing Extension.
Inventor has full 2.5 to 5-Axis capabilities, however it has fewer strategies available to it. The table below compares functionality between the two products and the Fusion Manufacturing Extension.
There is a large overlap in capabilities between Inventor and Fusion, Fusion begins to pull away from Inventor when it comes to some of the more complex toolpaths especially with the Multi-Axis functionality. However, Multi-Axis functionality, and some 3D Tools, in Fusion require the Manufacturing extension which is not included in the PDMC. So if this functionality were required it would mean the purchase of additional licensing.
For more information on this blog post, or if you have any other questions/requirements, please complete the below form:
Related Links
Autodesk Fusion – Man and Machine
Autodesk Fusion Training – Man and Machine
Autodesk Product Design and Manufacturing Collection – Man and Machine
Autodesk Fusion – Man and Machine
Autodesk Fusion Introduction to Parametric Modelling – Man and Machine
Autodesk Product Design & Manufacturing – Man and Machine
Autodesk Inventor – Man and Machine
Autodesk Inventor Training – Man and Machine
Autodesk Inventor CAM Training – Man and Machine
Inventor Training – Solid Modelling Introduction – Man and Machine
Autodesk Inventor – Autodesk Platinum Partner – Man and Machine