Once we are recording data within Fusion Operations day to day and building an accurate representation of our productions. We can begin to use this data to track and predict trends.
Using Analytics
Within Fusion Operations, we have access to an Analytics environment. This takes all the data we are already tracking, and places them into easily accessible graphs. These are customizable and can be filtered down by Production Order, Product, Product Category and various other properties. Which will track all our production trends, including Wastes or Finished products.
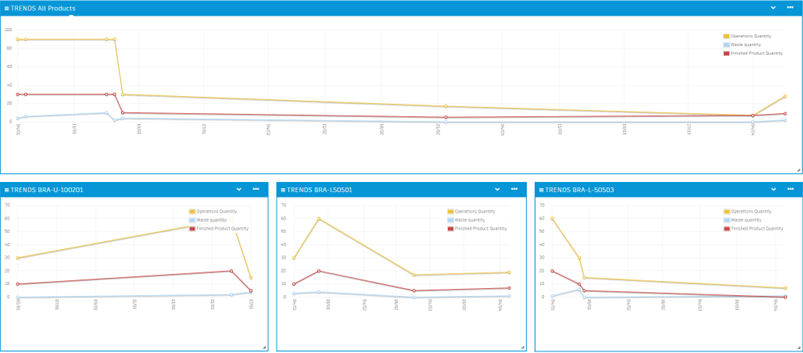
We can also adjust the date range to fine tune the results we are looking for. By doing so we can begin to trace either Monthly or Yearly trends in productions and orders.
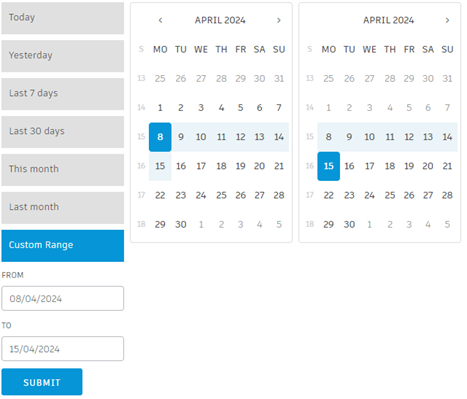
Adapting to Trends
Using this information, we can adapt our production based on potential product movements. Using resource planning and scheduling within Fusion Operations. Whereby we have the ability to track existing Stock levels, Projected demand and Existing orders. Within the Scheduling area we can use this data to ensure there is enough coverage at any level, whether it be material (Based on products), Work stations or workers.
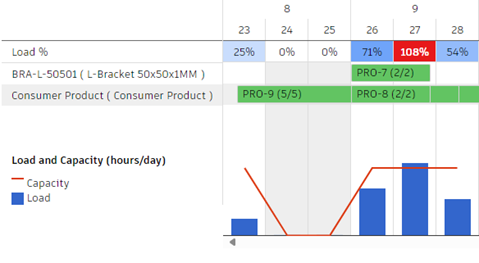
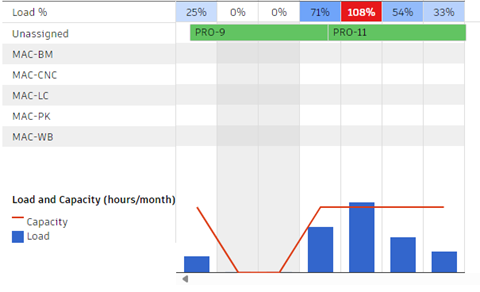
An added benefit to this, is the ability to plan for maintenance during quieter times.
For more information on this blog post, or if you have any other questions/requirements, please complete the below form: